About the author: John Meland is technical sales engineer for HaloKlear. Meland can be reached at [email protected].
The San Diego Freeway (I-405) is one of the most congested freeways in Los Angeles County, carrying more than 300,000 vehicle trips daily on some sections. The area’s population is expected to grow 11% by 2040, significantly increasing traffic volume on the freeway. The California Department of Transportation, in cooperation with the Orange County Transportation Authority, proposed widening I-405 by adding lanes in each direction to improve travel conditions, which would facilitate traffic flow and interchange operations and enhance road safety to meet state and federal standards.
This $721 million design-build project, in addition to adding lanes in each direction, included realigning existing on- and off-ramps, reconstructing or modifying 23 bridge and ramp structures, building approximately 18 miles of retaining walls, and performing road improvements on the adjacent city streets. The project began in 2013 and was completed in the first quarter of 2015.
Location & Excavation
One of the more challenging portions of the project involved the hydro-excavation required to locate utilities under the newly expanded portion of the freeway and surrounding areas. Kiewit was selected for the project and chose to use hydro-excavation to protect against unexpectedly hitting any utilities not properly recorded or not located exactly where maps stated, which could cause costly delays.
Hydro-excavation has become a favorite of construction companies working in older, high-density urban environments, as the process is less destructive and more accurate than traditional excavation techniques. Hydro-excavation removes soil with pressurized water. An air conveyance or vacuum then is used to transfer the soil/slurry from the excavation area to a disposal truck or tank.
In this project, the hydro-excavation trucks were filled with a combination of mud and rock. To protect the local ecosystem, the thick slurry byproduct could not be discharged on site. At the beginning of the project, Kiewit collected the slurry and transported it to an offsite facility that treated and disposed of it. “This process was completed at a cost of an estimated $3,000 per truck, and about 10 truckloads per day were loaded,” said Mike Pecsok of Rain for Rent.
Kiewit determined that it needed a solution to reduce its costs and recover the water for reuse in its hydro-excavation equipment, thereby reducing water used from the local water supply. These two goals, in addition to retaining the recovered dirt for use for the project’s backfill needs, were key to choosing an alternative treatment solution.
Kiewit consulted with Rain for Rent, which partnered with HaloKlear to develop a system for onsite slurry treatment, allowing the company to reuse the extracted water. Not only did the company drastically reduce its monthly treatment costs, but it also reduced its environmental impact by using a polymer and weir tank treatment system custom created on site for Kiewit.
The Solution
Rain for Rent and HaloKlear created a system to dewater the mud, effectively separating the solids from the water. After initial testing, HaloKlear recommended TW-10, a dry polymer product for dewatering sludge. As the dirt/water mix was pumped from the pre-settling tank, it was dosed with the TW-10 polymer, using a recirculating venturi system to introduce the dry polymer into the liquid stream. The treated slurry then was continually mixed in a tank that removed solids with a conveyor system. The sediment was flocked by the TW-10 polymer, then quickly settled to the bottom of the box. As the water rose to the top, it was easily removed from the box and pumped through BF400 bag filters to be reused on the clean water side of the hydro-excavation trucks. The solids on the bottom were removed from the tank using the unit’s energy-efficient scrapper-conveyor belt system. The dirt that was separated was further dewatered on site by spreading the solids on a concrete foundation to dry. It then was transported by dump trucks to be used elsewhere. The environmental impact was now considerably lessened, as transportation of the solids was minimized. Every 3,000 gal of slurry treated yielded approximately 1,800 gal of reusable water that went back into the hydro-excavation trucks.
“Rain for Rent adapted the standard rental equipment to keep the project on track while providing an engineered, custom system. It fit within the tight jobsite footprint without jeopardizing system functionality,” said Pecsok, who helped design the treatment system. The treatment area had a footprint of approximately 200 ft by 200 ft for all of the equipment. The 6,900-gal poly tank, BF400 and PF200 filters and scraper/conveyer tank system created a custom-designed system on an accelerated time schedule and worked well in this application.
Onsite Water Reuse
The process recovered more than 60% of the water used. As an added bonus, the water that came off the top of the treatment system was clear and had minimal turbidity of 4 ntu, making it suitable for reuse within the hydro-excavation equipment; water with higher turbidity risks damaging the sensitive high-pressure pumps used in the equipment. The ability to reuse the water reduced the need to tap into water resources drawn from the local hydrant. The reclaimed water thus was reused in the excavation equipment and for dust control throughout the construction site. The tanks were filled, treated and water was pumped off, then treated again. From a water use perspective, it was an ideal circular water reuse system.
After treatment, the solids concentration was improved from approximately 25% to 60% solids and the solids were easily moved using a backhoe. The solids were stored on site and used as backfill on the project. The company saved substantial treatment costs with this improved process while simultaneously minimizing its environmental impact in drought-ridden Southern California.
Download: Here
About the Author
John Meland
Related
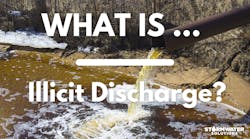