About the author: Mark Lister is regional sales manager, Weholite NE US, for KWH Pipe. Lister can be reached at 866.594.7473 or by e-mail at [email protected].
In August 2009, the Ohio Department of Transportation led the way, when it had the first 11-ft-diameter Weholite high-density polyethylene (HDPE) pipe installed in the U.S. for a culvert slipline application.
In 2004, Arcadis G&M, Cleveland, was awarded the design task for the LAK-2-2-3.32 project, with the primary purpose to enhance safety and reduce congestion on a 10-mile stretch of Rte. 2 in Lake County, Ohio. This stretch is designed for an annual daily traffic (ADT) of 68,000 vehicles, and once completed, it will be good for an ADT of 81,500. The project was divided into three phases, the second of which is currently under construction.
Phase II
This particularly complex section involves many bridge structures, ramps and a 15-ft-diameter, 1,000-ft-long corrugated metal pipe (CMP) culvert that has been extended an additional 260 ft with a 10-ft CMP culvert.
The culvert carries a tributary of the Chagrin River under Rte. 2, its interchange ramps and two local streets. The 15-ft CMP also had nine laterals, including one measuring 72 in. and another measuring 66 in. To address this challenging part of the project, Arcadis partnered with the Cleveland office of Parsons Brinckeroff (PB).
The 15-ft-diameter CMP culvert was built in 1962, with the 10-ft CMP added some years later. The culvert was inspected in 2005. The headwalls and 10-ft pipe were in good condition, but the 15-ft CMP needed major rehabilitation. Through the entire 1,000-ft length, extensive deterioration was found.
Deteriorating pipe called for rehabilitation.
Four options were considered:
1. Lining with smooth section pipes
2. A new culvert on the existing alignment with traditional cut-and-cover construction
3. A new culvert with new alignment using the cut-and-cover method
4. Tunneling a new culvert on new alignment
Options two and three were eliminated due to cost, public inconvenience and prolonged construction scheduling. Option four was eliminated due to the high expense of tunneling. The first option, the only viable option, led to four alternatives:
1. Lining with 11- and 8-ft polyethylene
2. Lining with 13- and 8-ft tunnel liner plates
3. Lining with 13- and 8-ft CMP
4. Lining with 11- and 8-ft reinforced concrete pipe
Alternatives two and three were dismissed because of cost and the corrugated nature of the interior of the plates and CMP. Alternative four was eliminated due to weight and the number of joints that would need to be sealed in the field. The 10-ft CMP was also to maintain hydraulic capacity.
“The HDPE liner solution presents the most viable option,” said PB Supervising Structural Engineer Phil Peterson. “It offers the least impact to the traveling public and provides the most easy and expedient construction process while minimizing potential risks to the owner and the contractor. In addition, it is less expensive than other options and at least is competitive with any other option.”
Polyethylene Solution
The first alternative was selected. It was at this time that KWH Pipe and D.A. Van Dam & Associates, Hubbard, Ohio, began providing Peterson with valuable information regarding Weholite large-diameter profile wall pipe. Profile wall pipe meeting ASTM F 894 is the only HDPE pipe with the capability of being manufactured to the large diameters required for this project and meeting the project requirements. The smooth inner diameter (n=0.01) and outer diameter that Weholite offers made it a leading contender from a shipping and installation point of view.
Smooth, large-diameter pipe met project needs.
Phase II was advertised and bid in late 2008. Great Lakes Construction and Anthony Allega Contracting were the successful joint bidders at approximately $86 million. The culvert relining was one portion of Phase II.
Weholite large-diameter profile wall pipe manufactured by KWH Pipe and sold through D.A. Van Dam was selected by the contractor. The pipe was provided in 42-ft lengths, with each piece weighing approximately 16,800 lb. Once connected, the pipeline would weigh about 400,000 lb. With a little ingenuity, Great Lakes was able to push the final pieces into the host culvert with a D7 and D8 dozer.
KWH Pipe and D.A. Van Dam technicians provided extrusion welding services. The entire 1,000 ft of 11-ft pipe was installed in 4.5 days, less than half the expected installation time.
“Weholite offered the most economical solution to the existing culvert problem without any disruption to existing traffic in the area,” said Arcadis Design Manager Ed Adamczyk.
About the Author
Mark Lister
Related
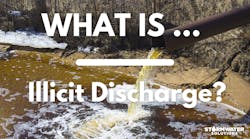